Spinning Machinery Market Size to Hit USD 9.78 Billion by 2034
The global spinning machinery market size is estimated to hit around USD 9 78 billion by 2034 increasing from USD 5 89 billion in 2024, with a CAGR of 5 20
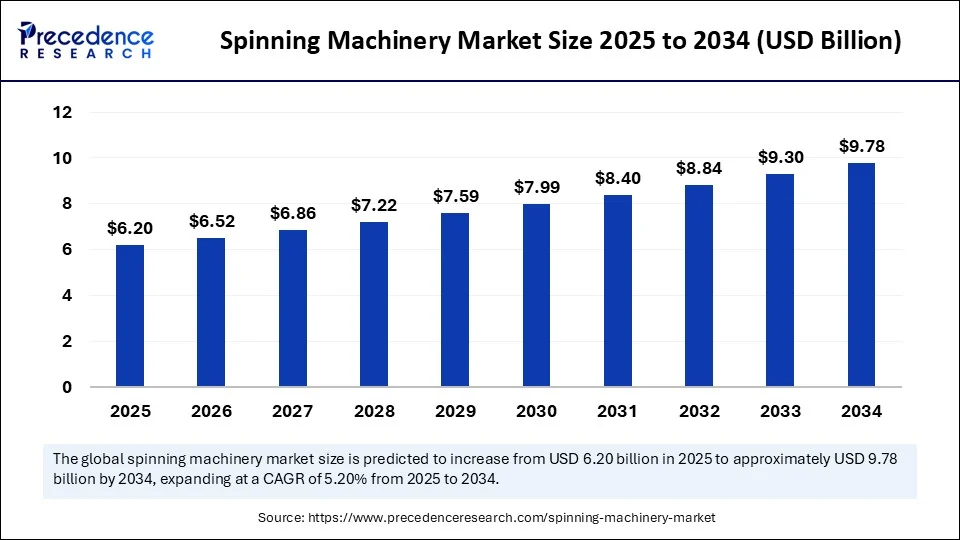
- In terms of revenue, the global spinning machinery market was valued at USD 5.89 billion in 2024.
- It is anticipated to reach approximately USD 9.78 billion by 2034.
- The market is forecasted to expand at a CAGR of 5.20% from 2025 to 2034.
- Asia Pacific dominated the market in 2024 and is projected to maintain its lead throughout the forecast period.
- Based on machine type, the ring spinning machine segment accounted for the highest share in 2024.
- The air-jet spinning machine segment is expected to register the fastest CAGR in the coming years.
- By operation type, the automatic segment led the market in 2024 and is likely to retain this position going forward.
- Regarding material type, natural fibers were the most widely used in 2024.
- The blended fibers segment is expected to grow at the highest CAGR during the forecast timeframe.
- By end-use industry, apparel & fashion remained the top segment in 2024.
- The industrial textiles segment is projected to experience the most rapid growth through 2034.
- Within spinning processes, the short staple spinning segment held the dominant market share in 2024.
- The long staple spinning segment is anticipated to grow at the fastest pace over the forecast period.
- By sales channel, direct sales accounted for the largest share in 2024.
- The online channels segment is poised to expand at the highest CAGR between 2025 and 2034.
Get Sample Link@ https://www.precedenceresearch.com/sample/6411
How is AI Transforming the Spinning Machinery Market?
Emerging technologies like artificial intelligence (AI) and the Internet of Things (IoT) are transforming the spinning machinery industry with groundbreaking advancements. These innovations enhance yarn quality, fabric precision, pattern design, color control, and optimize merchandising and supply chain processes. AI-powered systems automate critical tasks—from fiber handling to quality assurance—while machine learning algorithms analyze sensor data to predict equipment failures, enabling proactive maintenance and minimizing downtime.
AI also supports designers by enabling intuitive pattern creation with technologies such as 3D fabric visualization. Furthermore, fabric grading has become more accurate and objective through AI-driven processes. Artificial neural networks contribute to precise measurements of yarn characteristics, including fineness, staple length, and strength, significantly improving overall textile quality.
Market Overview
The global spinning machinery market, integral to the textile manufacturing industry, continues to evolve under the twin pressures of sustainability and digital transformation. Traditional ring spinning machines still dominate many mature markets, particularly in South and Southeast Asia, but newer technologies—such as compact spinning, open‑end (rotor) systems, and air‑jet spinning—are gaining ground.
The industry is seeing incremental modernization across spinning mills, with older equipment gradually phased out in favor of higher‑speed, automation‑friendly platforms. Market size is sizable, with demand closely tied to raw fiber availability (cotton, polyester, blends) and the geographic distribution of textile production hubs. While South Asia remains a powerhouse, China and Turkey maintain strong domestic systems. In parallel, new investments in Africa and Latin America are emerging, supported by rising apparel exports and reshored production for western markets.
Drivers
Several powerful factors are fueling market growth. First, global apparel demand continues to expand thanks to urbanization, population growth, and increasing per‑capita clothing consumption, prompting spinning mills to boost capacity and upgrade equipment. Second, effect of labor shortages and wage inflation, particularly in China, is accelerating automation adoption—spinning machinery with robotics, in‑line quality sensors, and self‑diagnostics reduces labor dependency.
Third, sustainability and circular economy initiatives push mills to acquire energy‑efficient, resource‑optimized spinning technologies that minimize power, water, and fiber waste. Fourth, the availability of better yarn types (e.g. high‑tenacity polyester, bamboo blends) drives demand for specialized spinning systems designed to maintain yarn quality at high speeds. Finally, government incentives and modernization schemes in textile‑producing economies (e.g. incentives for technology upgrades or emissions‑reduction hardware) provide additional impetus for machinery investment.
Opportunities
Opportunities in this market segment are rich and varied. Manufacturers can expand in upgrading legacy equipment in older mills, offering retrofit packages that boost performance at lower cost than full replacement. Technological upgrades that improve monitoring and predictive maintenance services—through IoT connectivity and digital twin platforms—create recurring revenue models via service contracts and software licensing.
Introduction of sustainable spun yarn varieties opens markets for specialized spinning systems—for example, systems optimized for recycled cotton or bio‑based fibers. Demand is growing in emerging and reemerging textile production regions such as Bangladesh, Vietnam, Ethiopia, and Pakistan, offering room for both machinery vendors and captive mill partnerships. Additionally, aftermarket services including calibration, spare‑parts, and operator training are increasingly important as mills upgrade their capabilities and seek to maximize uptime.
Challenges
Despite strong potential, the spinning machinery market faces important constraints. Capital intensity remains high—full‑scale line installations require substantial investment, which many small or mid‑sized mills find difficult to finance. Customization demands can be intense: different fiber inputs, yarn counts, and end‑product types necessitate tailored solutions, complicating manufacturing and support. Interoperability challenges arise due to inconsistent compatibility across legacy and modern equipment, hampering integration into digital systems.
Additionally, global commodity volatility—particularly raw fiber price swings—can disrupt mills’ investment cycles, delaying equipment upgrades. Trade barriers and tariffs (e.g. anti‑dumping duties, steel tariffs affecting machinery costs) may slow procurement in certain regions. Skilled manpower shortage is another issue: operating automated high‑tech spinning systems requires technically trained personnel, which is limited in some production hubs.
Recent Developments
In recent years, several leading spinning machine manufacturers have introduced fully automated compact spinning installations featuring in‑line yarn quality monitoring, adaptive tension control, and remote diagnostics. Some suppliers now offer end‑to‑end retrofit solutions: upgrading gearbox systems, drones‑style roll monitoring, and energy‑optimized drives to extend the life of older lines. Other innovations include open‑end rotor systems capable of producing fine-count rayon or recycled fiber yarn reliably at higher speeds, reducing energy per kg of yarn.
Digitization is advancing: IoT‑enabled spinning centers collect real‑time operational data, feeding into centralized dashboards for plant managers and enabling predictive maintenance alerts that reduce downtime. In parallel, aftermarket service models have emerged: manufacturers and third‑party service providers offer comprehensive service packages covering spare parts, training bootcamps, and optimization consulting.
On sustainability, a growing number of machinery lines comply with greener standards, consuming less electricity and supporting recirculating air or water systems to minimize environmental impact.
Spinning Machinery Market Companies
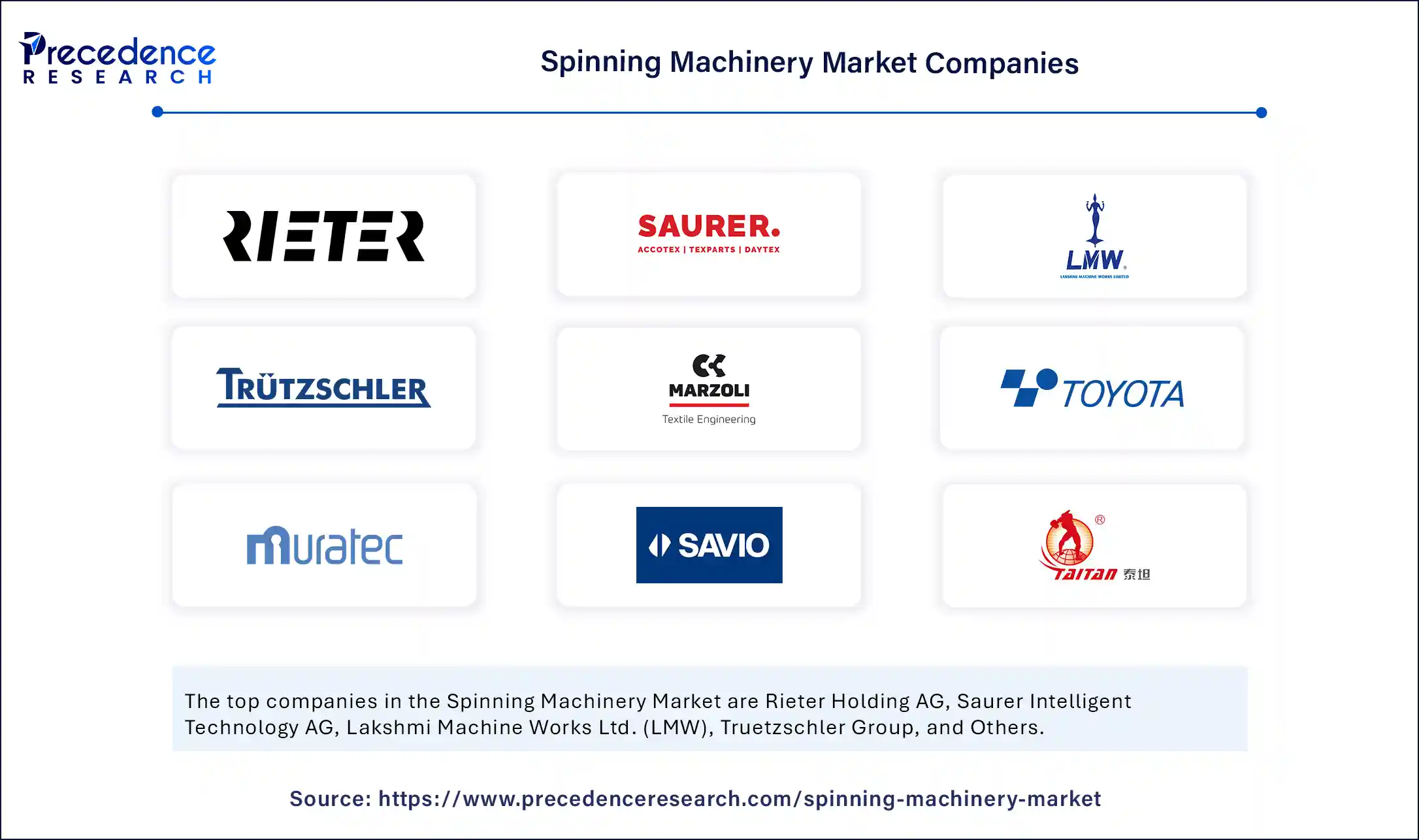
- Rieter Holding AG
- Saurer Intelligent Technology AG
- Lakshmi Machine Works Ltd. (LMW)
- Truetzschler Group
- Marzoli Machines Textile S.r.l.
- Toyota Industries Corporation
- Murata Machinery Ltd. (Muratec)
- Savio Machine Tessili S.p.A.
- Jingwei Textile Machinery Co., Ltd.
- Zhejiang Tatian Co., Ltd.
- Jiangsu Jinlong Machinery
- Electro-Jet S.A.
- SSM Scharer Schweitzer Mettler AG
- Perfect Equipements
- A.T.E. Enterprises
- Veejay Lakshmi Engineering Works Ltd.
- TMT Machinery, Inc.
- Pacific Associates
- Bhagat Textile Engineers Pvt. Ltd.
- Zhejiang Rifa Textile Machinery Co., Ltd.
Segments Covered in the Report
By Machine Type
- Ring Spinning Machine
- Rotor Spinning Machine (Open-End Spinning)
- Air-Jet Spinning Machine
- Friction Spinning Machine
- Others (e.g., Vortex, Electrostatic)
By Operation Type
- Automatic
- Semi-Automatic
- Manual
By Material Type
- Natural Fibers (Cotton, Wool, etc.)
- Synthetic Fibers (Polyester, Nylon, etc.)
- Blended Fibers
By End-Use Industry
- Apparel & Fashion
- Home Textiles
- Industrial Textiles
- Medical Textiles
- Automotive Textiles
- Others
By Spinning Process
- Short Staple Spinning
- Long Staple Spinning
By Sales Channel
- Direct Sales
- Distributors & Dealers
- Online Channels
By Region
- Asia-Pacific
- Europe
- North America
- Latin America
- Middle East & Africa
Also Read @https://www.precedenceresearch.com